Just how to Identify What is Porosity in Welding and Improve Your Strategy
Wiki Article
The Science Behind Porosity: A Comprehensive Guide for Welders and Fabricators
Understanding the complex devices behind porosity in welding is crucial for welders and fabricators striving for impressive craftsmanship. As metalworkers explore the midsts of this phenomenon, they discover a world governed by various factors that influence the formation of these minuscule voids within welds. From the structure of the base products to the complexities of the welding process itself, a plethora of variables conspire to either exacerbate or alleviate the presence of porosity. In this thorough overview, we will untangle the science behind porosity, exploring its effects on weld high quality and unveiling advanced methods for its control. Join us on this trip with the microcosm of welding blemishes, where precision satisfies understanding in the search of perfect welds.Recognizing Porosity in Welding
FIRST SENTENCE:
Evaluation of porosity in welding discloses crucial understandings into the honesty and high quality of the weld joint. Porosity, defined by the visibility of tooth cavities or voids within the weld steel, is a typical problem in welding procedures. These gaps, if not properly attended to, can compromise the structural honesty and mechanical properties of the weld, resulting in prospective failings in the finished product.
To spot and evaluate porosity, non-destructive screening methods such as ultrasonic testing or X-ray assessment are typically used. These strategies permit the recognition of internal issues without compromising the honesty of the weld. By examining the size, shape, and distribution of porosity within a weld, welders can make educated choices to improve their welding processes and achieve sounder weld joints.
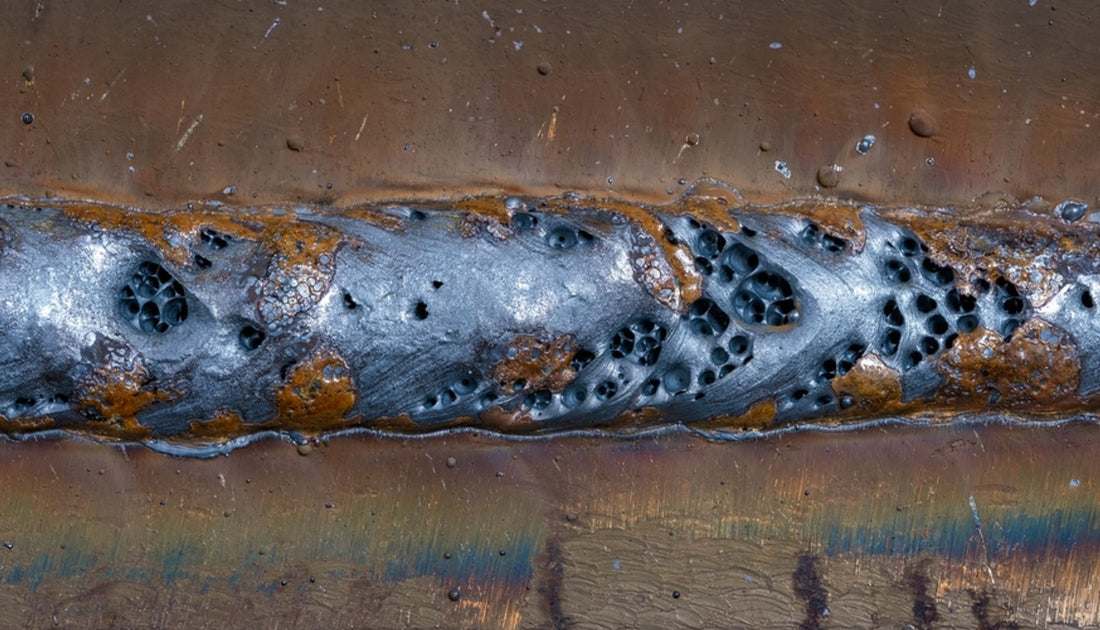
Factors Affecting Porosity Formation
The occurrence of porosity in welding is influenced by a myriad of aspects, ranging from gas protecting performance to the details of welding parameter setups. Welding criteria, including voltage, current, travel rate, and electrode kind, likewise influence porosity development. The welding method used, such as gas metal arc welding (GMAW) or shielded steel arc welding (SMAW), can influence porosity development due to variants in heat circulation and gas protection - What is Porosity.Results of Porosity on Weld Top Quality
Porosity formation considerably jeopardizes the architectural integrity and mechanical homes of bonded joints. When porosity exists in a weld, it produces voids or tooth cavities within the product, reducing the overall toughness of the joint. These gaps act as stress focus points, making the weld extra at risk to cracking and failing under tons. The existence of porosity additionally weakens the weld's resistance to deterioration, as the entraped air or gases within deep spaces can respond with the surrounding atmosphere, resulting in destruction in time. In addition, porosity can prevent the weld's capability to withstand pressure or influence, further jeopardizing the general quality and reliability of the bonded structure. look at this now In critical applications such as aerospace, automotive, or structural buildings, where security and durability are critical, the harmful results of porosity on weld quality can have extreme repercussions, highlighting the importance of reducing porosity with appropriate welding strategies and treatments.Techniques to Lessen Porosity
To boost the top quality of welded joints and guarantee architectural integrity, welders and fabricators employ certain techniques intended at lowering the development of voids and cavities within the material during the welding process. One effective approach to decrease porosity is to make certain correct visit site material preparation. This includes thorough cleansing of the base steel to remove any kind of pollutants such as oil, oil, or dampness that can add to porosity development. In addition, making use of the suitable welding criteria, such as the right voltage, present, and travel speed, is important in stopping porosity. Preserving a constant arc length and angle throughout welding additionally helps in reducing the chance of porosity.
Using the suitable welding technique, such as back-stepping or employing a weaving motion, can additionally assist distribute heat equally and decrease the opportunities of porosity formation. By applying these techniques, welders can effectively minimize porosity and create high-quality bonded joints.

Advanced Solutions for Porosity Control
Carrying out sophisticated modern technologies and ingenious approaches plays an essential role in accomplishing exceptional control over porosity in welding procedures. Additionally, utilizing sophisticated welding techniques such as pulsed MIG welding or changed ambience welding can additionally aid reduce porosity concerns.An additional innovative service entails making use of view publisher site innovative welding tools. Making use of tools with integrated features like waveform control and sophisticated power resources can improve weld high quality and decrease porosity risks. Moreover, the implementation of automated welding systems with accurate control over specifications can dramatically decrease porosity defects.
Additionally, incorporating innovative monitoring and inspection innovations such as real-time X-ray imaging or automated ultrasonic testing can help in finding porosity early in the welding procedure, enabling instant restorative activities. Overall, incorporating these innovative solutions can considerably improve porosity control and improve the overall top quality of bonded components.
Conclusion
In final thought, understanding the science behind porosity in welding is necessary for welders and makers to produce high-grade welds - What is Porosity. Advanced services for porosity control can additionally improve the welding process and make certain a strong and trustworthy weld.Report this wiki page